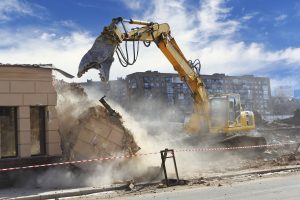
A high reach arm is used to demolish masonry structures and taller buildings from the top down.
When we think of building demolition, we often just think of a huge wrecking ball knocking down a building. While this is one of the methods that can be used, there are actually a variety of options when it comes to demolishing a building. The method that construction workers will use depends on factors such as location, building materials, and the purpose of the demolition. Here are four ways to demolish a building.
Implosion
This method of demolition is most often used for large buildings and structures that are in urban areas. It is the most dramatic method because it uses explosives to blow up a building’s vertical support structures, causing it to collapse from the inside out. In order for implosion to be successful, the demolition crew must closely analyze the structural blueprints of a building to figure out where the main structural supports are located.
High Reach Arm
With this demolition method, a base machine is used that an arm is then attached to. A demolition tool such as shears, a crusher, or a hammer are attached to the end of the arm. A high reach arm demolishes the building from the top down, removing large pieces of the building at a time. The crew then breaks those pieces down and disposes of them. High reach arms are used for masonry structures and taller buildings.
Wrecking Ball
Using a wrecking ball is the oldest and most common method of demolition. It is mostly used to demolish concrete structures, but can be used for other types of masonry structures as well. Wrecking balls can weigh up to 13,5000 pounds and are suspended from a crane. The ball can either be swung into the structure or dropped onto it. This requires a very skilled and experienced crane operator because of the size and weight of the wrecking ball.
Selective Demolition
Selective demolition is a newer demolition method and is rapidly increasing in popularity. This is because construction workers have the option to reuse or recycle some of the building’s materials. The goal of this method is to preserve as many reusable and recyclable materials as possible, making it a more costly and time consuming option.
Contact Del Prete Masonry Today for Your Demolition Needs!
If you are ready to upgrade your home or commercial building with professional masonry installation or replacement, Del Prete Masonry has the experience and expertise to get the job done right for the right price. To explore our residential and commercial services and set up a consultation, please give us a call at 410-683-0650 or contact us online. We currently serve Baltimore City and County, Harford County, Carroll County, Anne Arundel County, and Howard County. To see examples of our work and get more updates, follow us on Facebook, Twitter, Google+, and Pinterest.