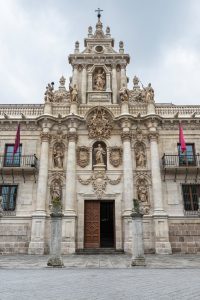
Masonry materials are made to last for years, but even the best projects can eventually start to deteriorate.
Masonry materials are some of the best to use for construction projects, giving buildings a timeless look and a long lifespan. However, even masonry deteriorates over time, meaning you will eventually need some repairs. Here are four potential causes of masonry deterioration.
Poor Design/Materials
Older buildings that were constructed from masonry materials may not have used the best quality materials or had the best design. New technology and upgrades allows us to have better quality buildings and materials. Man made materials as well as natural materials aren’t always the best quality which can lead to masonry deterioration. In addition to this, if the maintenance isn’t kept up with and repairs aren’t made when needed, it can speed up the deterioration process.
Corrosion & Secondary Materials
A lot of older masonry buildings incorporated secondary materials into the design for added support. Things like iron alloys are put into a lot of buildings to help make them sturdier. However, though it helps with sturdiness, these materials are way more susceptible to corrosion. Corrosion can affect the capacity of the material as well as put a lot of pressure on the rest of the masonry. If corrosion gets too bad, it can lead to deterioration and require very expensive repairs or even restoration.
Movement/Settlement
Over time, different natural factors can cause the building itself or the land underneath of it to move. Things like earthquakes or settlement of different materials over time can cause these movements. Masonry cracks are the first sign that there has been some type of movement in or around the building. You want to contact a professional if you notice masonry cracks so that they can help pinpoint the exact source, repair the cracks, and hopefully prevent them from recurring.
Moisture
Depending on what type of masonry materials are used for a building, moisture infiltration can be an issue. Masonry buildings are designed to resist damage from things like the sun and water. However, even a well designed building can be subject to water damage if it isn’t maintenanced correctly. You want to keep the mortar in good shape at all times, making repairs when necessary. As mentioned earlier, you also want to look out for any cracks as well and get them fixed as soon as possible. These things can lead to moisture getting into the masonry, causing masonry deterioration.
Contact Del Prete Masonry Today!
Whether you are ready to start your next masonry project or are still hesitant and have questions, Del Prete Masonry is here to help. We have the experience and expertise to get it right the first time. Questions? Want to visit some of our residential or commercial projects? Ready to set up a consultation? Feel free to give us a call at 410-683-0650 or visit us online. We are happy to serve Baltimore City and County, Harford County, Carroll County, Anne Arundel County, and Howard County. To see examples of our work and to keep up with our new and exciting projects, be sure to Facebook, Twitter, Google+, and Pinterest